Control valves play a critical role in regulating fluid flow in various industrial processes, ensuring precision and efficiency. Among the different types of control valves, globe style valves are widely used for their ability to provide precise control and tight shutoff. However, achieving good valve packing performance is crucial, especially in light of current fugitive emissions sealing requirements. This article explores the key considerations and best practices to ensure optimal performance in Globe style control valves while meeting stringent fugitive emissions standards.
Understanding Fugitive Emissions:
Fugitive emissions, or the unintended release of gases or liquids into the atmosphere, have become a significant concern in the industrial sector due to their environmental and safety implications. Regulatory bodies worldwide have introduced strict standards to control and minimize fugitive emissions, pushing industries to adopt technologies and practices that enhance sealing performance in control valves.
Key Factors Influencing Valve Packing Performance:
- Material Selection:
Choosing the right materials for valve packing is crucial for achieving optimal performance. High-quality, durable materials that can withstand the specific process conditions and maintain their integrity over time are essential. Common materials include flexible graphite, polytetrafluoroethylene (PTFE), and advanced composite materials. Here at MASCOT we use James Walker's top-of-the-range Supagraf Premium packing for valves.
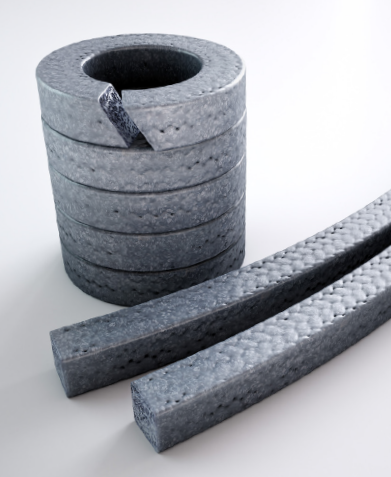
- Design Considerations:
The design of the packing system significantly impacts its performance. Engineers must consider factors such as the number of packing rings, the type of packing arrangement, and the pressure and temperature conditions. Proper design can minimize friction, reduce wear, and enhance sealing capabilities.
- Preventive Maintenance:
Regular maintenance is essential to ensure the longevity and efficiency of the packing system. Periodic inspections, adjustments, and replacements of worn components can prevent leaks and maintain the integrity of the valve packing.
- Installation Practices:
The correct installation of valve packing is often overlooked but plays a crucial role in its performance. Following manufacturer guidelines, using proper tools, and ensuring that all components are correctly aligned and tightened are essential steps in achieving effective sealing.
Meeting Fugitive Emissions Sealing Requirements:
- Compliance with Standards:
Fugitive emissions standards, such as those set by the Environmental Protection Agency(EPA) in the United States or the International Organization for Standardization (ISO), must be strictly adhered to. Compliance involves selecting packing materials and designs that meet or exceed these standards.
- Advanced Sealing Technologies:
Innovations in sealing technologies, such as the use of live-loaded packing systems and low-emission packing designs, can significantly reduce fugitive emissions. These advancements focus on minimizing friction, enhancing durability, and improving overall sealing performance.
- Testing and Certification:
Rigorous testing and certification processes help validate the sealing performance of Globe style control valves. Manufacturers should provide documentation proving that their valves meet or exceed fugitive emissions standards, giving end-users confidence in the reliability of their equipment.
Achieving good valve packing performance in Globe style control valves while meeting current fugitive emissions sealing requirements is a multifaceted task that involves careful consideration of materials, design, maintenance, and compliance with standards. As industries continue to prioritize environmental sustainability and safety, investing in high-quality sealing solutions and staying abreast of technological advancements will be key to ensuring optimal valve performance and minimizing fugitive emissions.