What is a choke valve?
A Choke valve is a mechanical device that induces restriction in a flow line, causing either a pressure drop or a reduction in the rate of flow. In the context of the upstream oil and gas industry, Choke valves are used wherever there is a requirement for wellhead flow and pressure control.
What are the main parts of a choke valve?
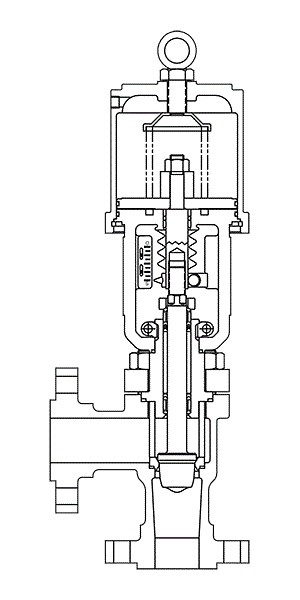
What are the main types of choke valves?
A positive Choke has a fixed orifice size. Although fixed chokes are available in a wide variety of sizes and types, the Choke must be disassembled to change bean sizes. The term ‘bean’ refers to the piece of hardware installed in the line that has an orifice, or opening, drilled into it. The bean size is the inside diameter (ID), or bore, of the fixed orifice. These bores are available in 1/64th of an inch increment.
An adjustable Choke provides variable orifice sizes through some type of external adjustment device, such as an actuator. This arrangement will accommodate a range of conditions, from a uniform pressure drop to a variable inlet pressure drop.
An injection Choke is used to control water, gas or chemicals injected back into the well to force/stimulate oil or gas to the surface or aid flow assurance. It should be noted that surface choke valves are rarely mounted vertically, contrary to popular belief. They are much more likely to be mounted so that flow arrives from the side.
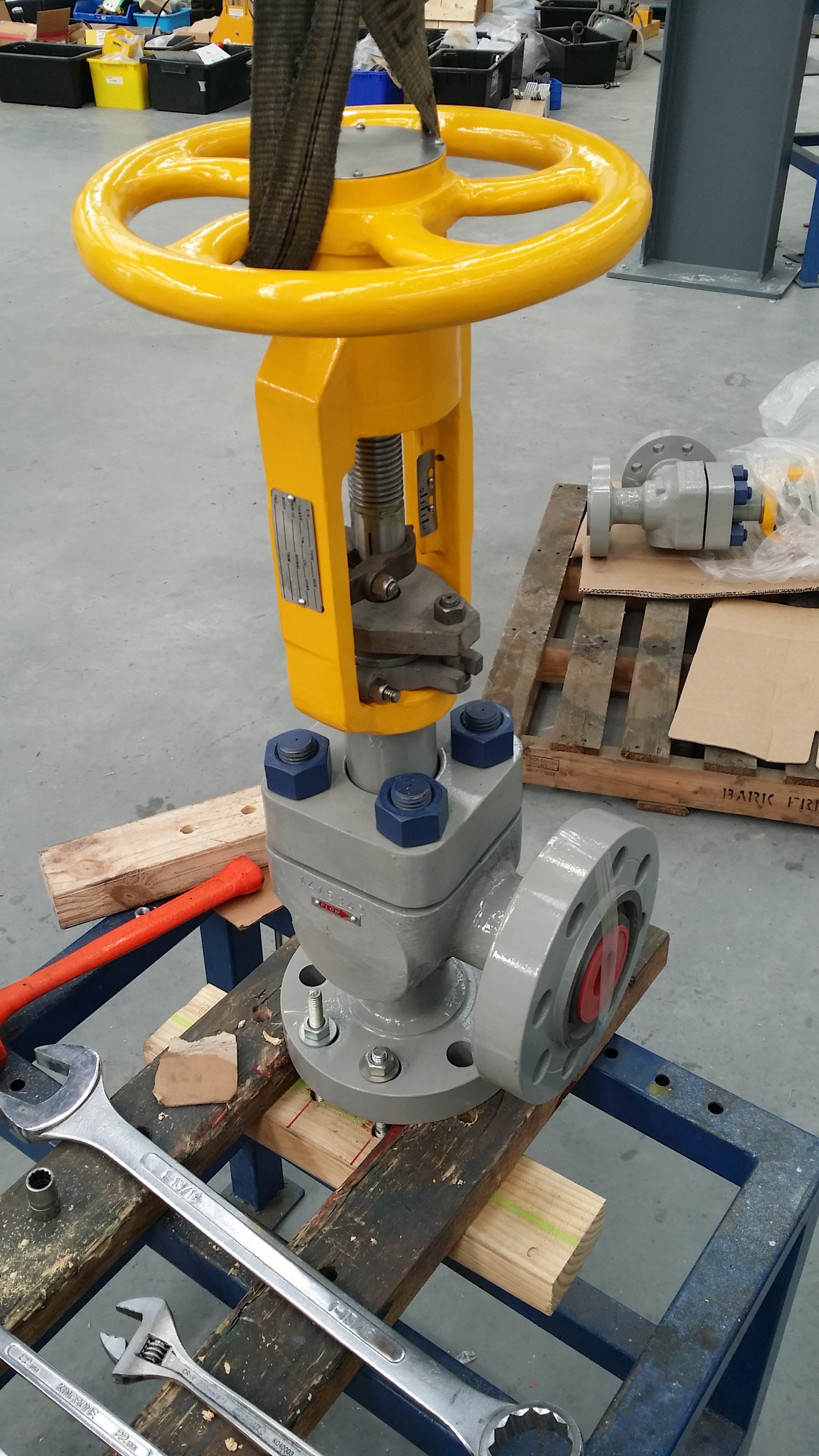
Choke Valve Trim Types (Simplest to Most Complex)
1. Needle and seat
- Simplest and least expensive adjustable choke valve
- Good pressure control for low DPs
- Reasonable capacity
2. Multiple orifice valve
- Quick open and close (90)
- Good flow rate and pressure control
- Available as in-line installation
3. Fixed bean
- Best for applications requiring infrequent adjustments
- Used mostly on wellhead Christmas trees
4. Plug and cage
- High capacity
- Good controllability
5. External sleeve
- Best for applications requiring infrequent adjustments
- Used mostly on wellhead Christmas trees
What are the main applications of choke valves?
- Oil production platforms
- Gas production platforms
- Surface wellheads
- Subsea trees
- Surface manifolds
- Subsea manifolds
- Onshore oil wells
- Floating production, storage and offshore loading vessels
What are some common issues with choke valves?
1. Corrosion
Valves are designed typically with a 20-year life. However, in this time, the whole valve would corrode because of a chemical reaction to the seawater. To counteract the effect of galvanic corrosion (the proximity of dissimilar metals to each while in water), cathodic protection is used.
2. Flashing
When oil and gas combine, they act as a liquid, having a vapour pressure (VP). If the local static pressure falls below the fluid VP, vapour bubbles are generated within the liquid – known as flashing. If the downstream static pressure remains below the fluid VP, then these vapour bubbles will remain in the downstream flow, causing erosion. To overcome this phenomenon, the correct materials must be selected, and the application designed to maintain flow at the correct velocity.
3. Cavitation
Even when the outlet pressure is higher than the VP, problems might still arise. If the pressure drops, allowing the liquid to become a gas and bubbles to form – these bubbles will collapse when returning to a liquid state. As this happens, the bubbles tear away at the material used in the valve – this could potentially ruin a valve in a matter of hours, if unchecked. The solution here is to use a low-recovery valve trim and to drop the pressure carefully using trim technology. This will eliminate cavitation and reduce flow velocity to prolong the life of the valve while maintaining an acceptable production rate.
This is where our anti-cavitation trim and valve design can prevent this issue.
4. Erosion
This takes place when physical materials such as sand are present in the pipeline. Using solid carbide would protect against sand erosion, but a stray piece of stone or rock would be likely to shatter such a fragile material. Steel outer cages known as brick stoppers are placed to avoid this. Fluid velocities being kept low also mitigate erosion rates.
Other key problems include the following:
- Pipe vibration
- Noise (indication of excessive vibration)
- Poor control
- System shut-down demands
- Trim and body wear
Why should you choose a MASCOT Choke Valve?
GFLO Choke valves offer superior performance and erosion protection in high pressure drop liquid, gas and 2-phase flow applications.
The GFLO Choke Multi Orifice trim consists of carefully engineered diametrically opposed holes that are designed to divide the process into several flow streams. These flow streams are directed into the center of the trim, where opposing streams collide, dissipating the throttling energy within the flow stream itself at the center of the trim, away from valve components.
Do you need help deciding what type and size of valve you need? Try out our valve Sizing Software or get in touch with us for a quote.
MASCOT Industrial engineers have over 100 years of combined experience in providing high quality equipment to the Global Continuous Process Control Industry. Our core products and services include control valves, choke valves, actuated and commodity valves, and associated equipment for both standard and severe service applications.
Our Engineering & Manufacturing expertise allows us to provide tailored solutions to our customers’ needs with timeliness and accuracy no matter the process. We aim to exceed our expectations with Better Value highly engineered products, faster delivery on any process, offering support from first contact through to after-sales and beyond.
For more information about our services, please call us at +61 3 9608 6400 or get in touch via sales@mascot-industrial.com
You might also want to check our related posts.