What are the different components of a control valve?
- Body
It is a type of a pressure vessel containing an orifice or an opening. The controlled liquid is allowed to flow through the body of the valve. It helps to monitor the flow regulation behaviour.
- Trim
Besides the body, trim is one such part of the valve that comes directly in contact with the fluid. It consists of the seat, disc, plug, and stem.
- Actuator
It consists of electric or pneumatic or hydraulic mediums to provide the force required to operate the control valve.
- Bonnet
It provides a mounting for the guide and actuator and a medium for the stem to pass through. It is made of the centrepiece, packing, packing nut and guide. The packing acts as a fastener between the bonnet and stem. It helps to avoid any leakage.
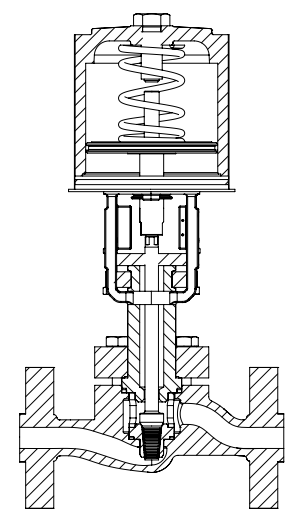
What are the Working Principles of a Control Valve?
- Pneumatic Actuated
Pneumatic Actuators use an air or gas signal from an external source to produce a modulating control action. The actuator receives the force of the pneumatic signal through a top port. Then, it distributes the signal across the actuator’s diaphragm. As a result, the actuators exerts pressure on the closing member. This moves the valve stem downward in a way that strokes the control valve.
- Electric Actuated
They are motor-driven devices. They use an electrical signal that can help create a motor shaft rotation. This movement is converted into a linear motion, which helps to drive the stem in the valve for flow modulation.
- Hydraulic Actuated
Hydraulic actuators are similar in operation to pneumatic actuators except they use a fluid, hydraulic oil, as the signal fluid to control the action of the valve. They are used, in place of pneumatic or electric actuated valves when the force required to move the valve stem is high.
How Does a Control Valve Affect the Control Loop?
Process plants consist of many control loops, networked together to produce a product. The control loops are devised to keep essential process variables such as fluid level, pressure, and temperature within the specified limit. This helps to ensure that the quality of the end product is as desired. Each of these loops creates internal disturbances that may affect the process variables.
Sensors and transmitters are used to collect information about the process variable. A control valve is an end device used to control the process based on this data. This helps to decide the course of action to get the process variable back to where it should be (set point).
MASCOT Industrial engineers have over 100 years of combined experience in providing high quality equipment to the Global Continuous Process Control Industry. Our core products and services include control valves, choke valves, actuated and commodity valves, and associated equipment for both standard and severe service applications.
MASCOT’s Engineering & Manufacturing expertise allows us to provide tailored solutions to our customers’ needs with timeliness and accuracy no matter the process. We aim to exceed our expectations with Better Value highly engineered products, faster delivery times on any process, offering support from first contact through to after-sales and beyond.
For more information about our services, please call us at +61 3 9608 6400 or get in touch via our website.
If you enjoyed this article, you may also like to read Control Valve Basics: Types, Applications and Parts.